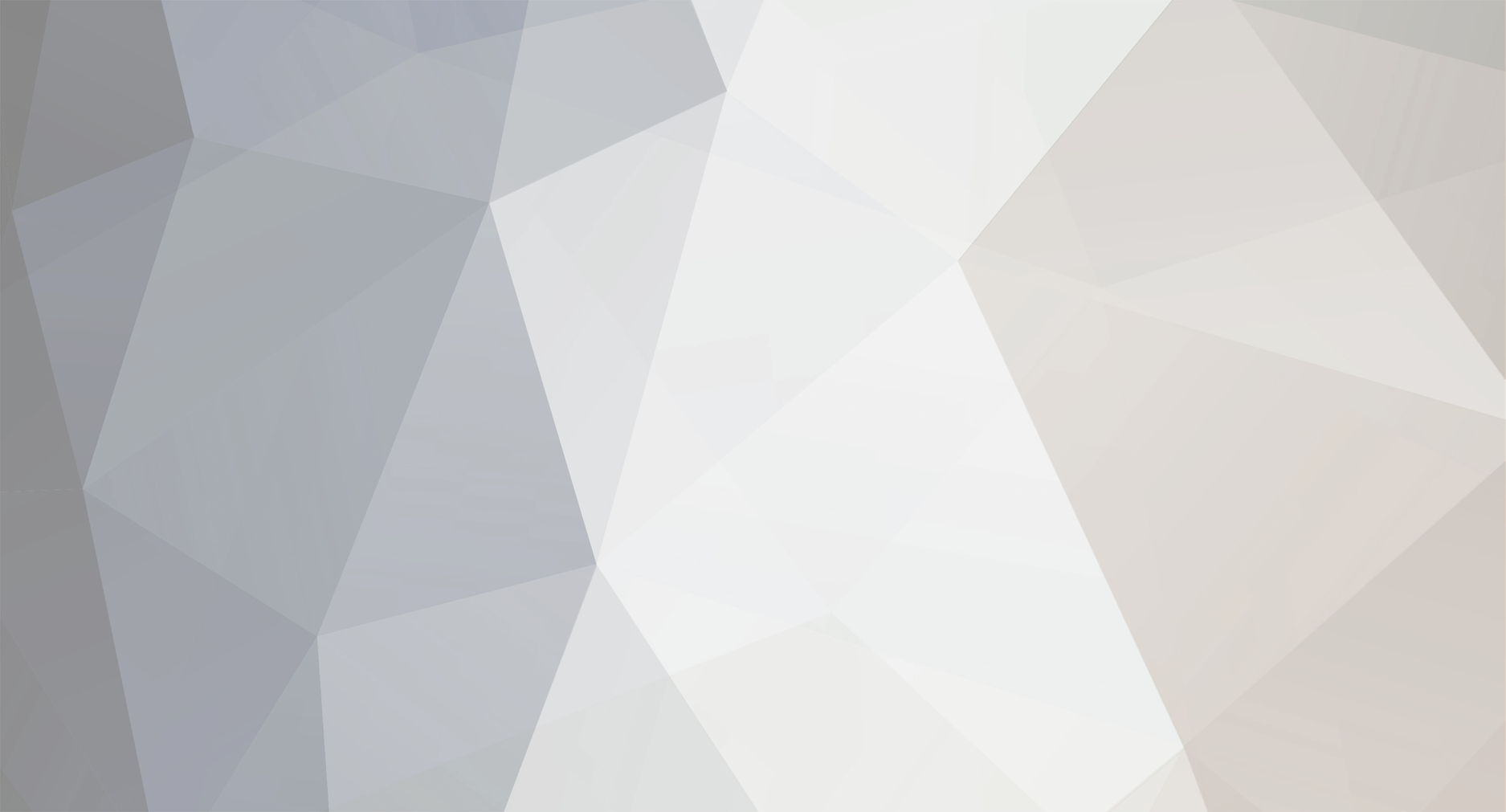
stampa3D
Membri-
Numero contenuti
8 -
Iscritto
-
Ultima visita
Tipo di contenuto
Profili
Articoli
Introduzione alla stampa 3D
Database materiali
Forum
Calendario
Blogs
Gallery
Download
Store
Tutti i contenuti di stampa3D
-
- Pubblicazione comunicato stampa del 24 agosto 2018 - Come risposta all’utilizzo crescente dei compositi nei vari settori, Stratasys (Nasdaq:SSYS) ora offre un sistema di fabbricazione additiva a basso costo dedicato al Nylon 12 caricato a fibra di carbonio. La stampante Fortus 380mc edizione a fibra di carbonio, presentata in anteprima in occasione del RAPID 2018, è un sistema di livello industriale, con un costo a partire da 70.000 euro nell’area EMEA, e sarà venduto in questa regione nelle prossime settimane. Stratasys Fortus carbonio - Le richieste del mercato Di recente, il materiale composito ha assistito a una crescita sul mercato anno dopo anno dall ‘8 al 12%. Le applicazioni composite in fibra di carbonio e i polimeri rinforzati in fibra di carbonio sono considerati tecnologie energetiche pulite dal Dipartimento dell’Energia degli Stati Uniti d’America in quanto consentono di produrre oggetti più leggeri, i quali riducono il consumo di energia. Si stima che una riduzione del 10% del peso del veicolo consenta di ridurre dal 6 all’8% il consumo di carburante. STAMPA 3D METALLO “DIRECT METAL PRINTING”: COS’È E COME FUNZIONA Stratasys è stata una delle prime aziende a offrire un composito caricato a fibra di carbonio per la fabbricazione additiva, ma in precedenza offriva il materiale solo sulle stampanti 3D di produzione di fascia alta, tra 200.000 e 350.000 euro. “I nostri clienti spingono per un accesso semplificato alla fibra di carbonio”, afferma il vicepresidente senior di Stratasys, Pat Carey. “Ci hanno detto che desiderano una soluzione a basso costo ma in un sistema affidabile di livello industriale. È per questo che stiamo offrendo un sistema più accessibile, basato sulla nostra piattaforma Fortus 380. Poiché la 380mc CFE è dedicata esclusivamente al Nylon 12 caricato a fibra di carbonio e a un altro materiale, siamo in grado di offrirla al prezzo più basso di qualsiasi altra stampante industriale”. “Da molti anni, il settore della fabbricazione additiva assiste alla necessità di una serie di macchine diverse per produrre parti in materiali compositi a resistenza elevata” afferma Terry Wohlers di Wohlers Associates, un’azienda di consulenza nel settore della fabbricazione additiva. “Spero che la recentissima macchina di Stratasys consentirà di soddisfare questa esigenza offrendo parti resistenti in fibra di carbonio e Nylon 12”. POLIAMMIDE 11 – MATERIALE IN POLVERE PER LA STAMPA 3D A SINTERIZZAZIONE LASER Il team Penske utilizza l’FDM per produrre prototipi e parti finali nel materiale composito Nylon 12 caricato a fibra di carbonio sia per le auto da corsa dell’IndyCar che per quelle della NASCAR. Il team ha utilizzato di recente il composito per produrre un alloggiamento per lo specchietto per i team di corsa della NASCAR. Dopo aver progettato l’alloggiamento, gli ingegneri hanno personalizzato il progetto per ognuno dei piloti dei bolidi, creando le parti finali in composito tramite FDM. Il materiale basato su fibra di carbonio ha consentito al team Penske di produrre alloggiamenti per specchietti leggeri con elevata resistenza agli urti e alta rigidità, caratteristiche fondamentali nel settore delle corse. La rigidità del composito è vantaggiosa soprattutto quando si creano parti con pareti sottili, che non devono flettersi sotto i carichi aerodinamici prodotti sulla pista. Le applicazioni additive per il Nylon 12 caricato a fibra di carbonio possono includere: Prototipazione funzionale delle parti in composito o in metallo Cicli di produzione brevi in un materiale a resistenza elevata Produzione di strumenti di assemblaggio leggeri per migliorare l’ergonomia e alleviare la fatica degli addetti Sostituzione di parti metalliche con compositi leggeri e resistenti Stratasys prevede che i più rapidi ad adottare la stampante 3D Fortus 380 CFE saranno le aziende che realizzano strumenti e staffaggi e le aziende dei settori automobilistico, delle attrezzature per gli sport ricreativi, marino, ortesico e protesico, della difesa, aerospaziale, delle attrezzature mediche, del petrolio e del gas. Come una parte in plastica rinforzata con fibra di carbonio stampata a iniezione, il Nylon 12CF di Stratasys è costituito per il 35% di frammenti di fibra di carbonio e presenta un rapporto rigidità/peso elevato, superiore a qualsiasi parte stampata in 3D FDM o FFF.Stratasys Fortus 380mc CFE si basa su una piattaforma comprovata che produce parti caratterizzate da precisione dimensionale ripetibile. Le parti non mostrano curvatura o restringimento apprezzabile e mantengono una stretta tolleranza. Il Nylon 12CF Stratasys è fino a quattro volte più resistente rispetto all’alternativa economica sull’asse delle X e delle Y e mantiene le proprietà meccaniche a una temperature superiore del 40%. STRATASYS PER LA STAMPA 3D DENTALE: LA NUOVA J700 DENTAL Stratasys Fortus 380mc CFE crea parti dello spessore di 0,254 mm (0,010 pollici). Il sistema è inoltre compatibile con la termoplastica ASA, che è in grado di produrre spessori degli strati di 0,127 mm (0,010 o 0,005 pollici). La camera di costruzione della stampante 3D misura 355 x 305 x 305 mm (14 x 12 x 12 pollici). Offre la rimozione del materiale di supporto idrosolubile, che elimina la necessità di manodopera per la rimozione dei supporti. Di conseguenza, consente la creazione di geometrie sottili e intricate, che sarebbero impossibili senza il materiale di supporto solubile, in quanto le caratteristiche sottili verrebbero distrutte durante la pulizia oppure la rimozione del materiale di supporto dalle geometrie intricate potrebbe risultare troppo laboriosa o addirittura impossibile. La stampante 3D Fortus 380mc edizione in fibra di carbonio sarà visibile presso lo stand Stratasys in occasione del TCT #H36 dal 25 al 27 settembre al NEC di Birmingham. Vuoi saperne di più? Iscriviti al nostro forum, la community sarà felice di aiutarti! Resta aggiornato sulle ultime novità, seguici su Facebook e Twitter.
-
- stampanti 3d
- settori
-
(and 3 più)
Taggato come:
-
Al ritorno dalle vacanze estive arriverà il momento di organizzare la prossima stagione lavorativa al meglio, fondendo momenti di puro lavoro e formazione. Esatto, formazione. Sappiamo entrambi quanto sia importante tenersi aggiornati sulle ultime tecnologie e il beneficio che queste possono apportare a livello professionale/lavorativo. Chi dorme non piglia pesci, dicevano. Ecco perché ho deciso di condividere già da adesso l'opportunità di iscriversi al prossimo corso di stampa 3D che terrò nel mese di settembre. Corso di stampa 3D @ FORMart Bologna - Info generali Due giorni interi dedicati alla stampa 3D, impostati sul format di successo già proposto ai corsi tenutosi a Modena e Bologna in marzo e maggio 2018. A differenza dei corsi precedenti, ai quali si potevano iscrivere solamente aziende facenti parte di specifiche categorie merceologiche, l'iscrizione a questo corso sarà aperta a tutte le categorie. Un'occasione unica, che non potrà essere replicata con alta frequenza. Si riparte quindi da Bologna, il 21 e il 28 settembre, con un nuovo corso organizzato in collaborazione con FORMart, che ci offrirà gli spazi e l'appoggio organizzativo, e SI-Design, fidato partner tecnologico che metterà a disposizione stampanti 3D FDM, DLP, materiali di consumo e scanner 3D. Corso di stampa 3D @ FORMart Bologna - Temi trattati Il corso è finalizzato all'apprendimento dell'utilizzo delle stampanti 3D FDM - Fused Deposition Modeling - e DLP - Digital Light Processing - attraverso la produzione di modelli in tempo reale e lo studio dei parametri di stampa tramite software di slicing. Saranno analizzate una serie di case history di successo, esaminando le tecnologie, i materiali e i processi di produzione utilizzati, arrivando alla definizione di quella che è la toolchain per la stampa 3D di livello professionale. Infine, giusto per non farci mancare niente, potremo vedere insieme l'utilizzo di scanner 3D in funzione del reverse engineering. I contenuti del corso sono targetizzati per soddisfare le richieste di aziende e professionisti. Riassumendo, nel corso vedremo questi temi: Introduzione alle tecnologie di stampa 3D Produzione di modelli 3D tramite modellazione e scansione 3D Materiali utilizzabili Case History di successo Software Slicing: parametri di stampa e analisi di casi particolari Approfondimento tecniche additive FDM e DPL Toolchain per la produzione e la prototipazione Tipologia di scanner 3D, software e funzionalità Il reverse engineering Per la scelta di una stampante: garanzia di qualità, ricambi, assistenza, ripetibilità della stampa. Corso di stampa 3D @ FORMart Bologna - Iscrizioni La quota di partecipazione è di € 300 + iva e il termine per le iscrizioni è fissato in data 17 settembre 2018. Il corso prevede il ricorso ad esercitazioni ed applicazioni pratiche in laboratorio informatico. Arrivati a termine sarà rilasciato un attestato di frequenza. La sede di svolgimento del corso è FORMart Bologna, via Ronco n.3, Castelmaggiore (BO). Per iscriverti puoi scrivermi all' indirizzo info@stampa3d-forum.it. Non aspettare, i posti sono limitati! Non perdiamoci di vista: clicca qui per iscriverti al nostro forum! Resta aggiornato sulle ultime novità, seguici su Facebook e Twitter.
-
Recensione PLA EUMakers - Un produttore ricco di sorprese
stampa3D ha pubblicato un articolo in Recensioni
Per le stampanti 3D FDM, il filamento è come un compagno di viaggio: va sempre scelto con cura, altrimenti rischi che vada a rovinare la vacanza. Il filamento, infatti, è uno degli elementi fondamentali per ottenere buoni risultati nella produzione dei modelli tramite stampa 3D FDM. La qualità del filo, come anche la sua composizione chimica, definiscono quelle che saranno la resistenza e la finitura dell’oggetto finale. Detto questo, è facile capire quanto la scelta delle materie prime e la produzione influiscano sulla buona riuscita delle nostre stampe, ed è proprio per questo motivo che deve essere scelto con molta cura. Tra i vari produttori di tutto il mondo, uno in particolare si contraddistingue per la grande disponibilità di colorazioni: stiamo parlando di un offerta pari a 57 filamenti diversi di PLA. Recensione PLA EUMakers - Il PLA curato nei minimi dettagli Il PLA di EUMakers si presenta all’interno di scatole in cartone protette da una pellicola trasparente in plastica. La scatola riporta le caratteristiche del filo: tipologia di materiale, diametro, peso, colore, temperatura di estrusione consigliata sono le informazioni che è possibile avere già direttamente dall’esterno della confezione. La bobina è a sua vota sigillata all’interno di una confezione in plastica sottovuoto e contenente un sacchettino di sali, utili per assorbire l'umidità che potrebbe rovinare il filo. Di conseguenza, il materiale arriva a casa come se fosse appena uscito dall’estrusore di filamento in azienda, mantenendo le sue proprietà inalterate. Un primo pensiero devo dedicarlo al confezionamento della bobina è di ottima qualità: la presenza di tutte queste accortezze da parte del produttore dimostra la conoscenza delle problematiche relative al progressivo degenero della qualità della plastica se lasciata all’aria aperta. Tutti questi dettagli fanno pensare di avere sottomano un materiale di una qualità. La stampante utilizzata per effettuare questo test di stampa è una GiMax Maty vecchio modello, con ugello da 0.4 mm e dotata di due ventole di raffreddamento del filo appena estruso. Recensione PLA EUMakers - Test di stampa 1: case per controller Il primo oggetto che ho deciso di stampare con i filamenti EUMakers è un semplice case per un controller elettronico. Si tratta di un pezzo semplice, con una piccola parte a sbalzo e avente funzione di raccogliere al suo interno piccole parti di elettronica. L'altezza dei layer utilizzata in questa prima prova è di 0.2 mm. Il materiale ha aderito bene al piano di stampa in vetro (con una spruzzata di lacca Splendor e riscaldato a 30 °C) senza dare alcun segno di ritiro. Il pezzo è venuto sufficientemente rigido e senza imperfezioni. Anche le parti più piccole hanno soddisfatto le mie aspettative. Recensione PLA EUMakers - Test di stampa 2: telaio per drone Stampato a 0.1 mm di altezza dei layer, anche in questo caso i risultati sono stati più che buoni. Il materiale, estruso a 205 °C con piano freddo, non ha dato segni di ritiro o deformazione, pur essendo le pareti del modello molto sottili. Le imperfezioni che potete notare sulle superfici a vista non sono dovute al filamento, ma piuttosto a una velocità troppo elevata di esecuzione della stampa - errore mio! Anche le parti composte da sezioni molto piccole si sono dimostrate ben prodotte, senza presentare problemi di rottura o delaminazione. Qui lascio il link al modello 3D, scaricabile da Thingiverse. Recensione PLA EUMakers - Test di stampa 3: moschettoni Per il terzo ed ultimo test, l’oggetto stampato è stato qualcosa che volevo fare da tempo. I moschettoni che vedrete nelle prossime immagini sono composti da due elementi che vengono incastrati uno dentro l’altro. Grazie alla flessibilità del PLA è possibile usare questo oggetto come se fosse stato prodotto in modo tradizionale. In questo caso, ho deciso di stampare due modeli. Il primo è stato prodotto con due normali PLA - Blue Metallic e Pearl White. Stampa a 0.2 mm di layer, infill al 100%: la resistenza e la flessibilità dell’oggetto finito sono notevoli. L’elemento dotato di rotazione tende a deformarsi dopo un utilizzo abbastanza sostenuto - se ci giochicchiate con le dita in modo costante vedrete che non riuscirà più a scattare in posizione di chiusura come se fosse nuovo. Ma questo è normale, il PLA è un materiale che si deforma, non mi aspettavo un comportamento diverso. Il secondo moschettone è stato stampato usando due PLA riciclati presenti nell’offerta commerciale di EUMakers - i due di colore verde, ZLife e Bio. Il risultato mi ha colpito in positivo: a parità di parametri di stampa, i materiali hanno risposto in modo del tutto simile a quello dei materiali non riciclati. Al tatto il filamento si presenta più morbido, anche se in modo quasi impercettibile. Dopo aver messo sotto stress il moschettone, ci ha mollato un po’ prima rispetto al modello precedente. Dopotutto è normale: non potevamo aspettarci da un materiale riciclato una resistenza e deformazioni migliori rispetto a un materiale estruso per la prima volta. Recensione PLA EUMakers - Conclusioni Il questa recensione il PLA EUMakers ha sbalordito in modo molto positivo. La cura ai dettagli e la conservazione del filo dimostrano la volontà di consegnarlo integro ai consumatori. Le plastiche hanno comportamenti di qualità e, la grande possibilità di scelta nelle colorazioni, può soddisfare le richieste più bizzarre. Anche una volta estrusi, i colori restano sgargianti e fedeli a quelli proposti dalla confezione. Inoltre, l'azienda fornisce idee creative che permettono di riutilizzare il rocchetto della bobina, una volta che il filamento è finito. In questo modo, gli scarti di plastica si riducono, permettendoci comunque di ricavare un oggetto utile e utilizzabile tutti i giorni. Tirando le somme, EUMakers si è dimostrato un produttore ricco di sorprese, capace di consegnare materiali di qualità. Se volete provare anche voi i PLA EUMakers, potete visitare il sito internet dell'azienda. -
In data 18 Giugno Lumi Industries, start-up italiana che progetta e produce soluzioni innovative nell’ambito della stampa 3D a resina, ha annunciato il lancio di una nuova campagna su Kickstarter per il suo ultimo progetto: VVD visualizzatore volumetrico tridimensionale. VVD visualizzatore volumetrico tridimensionale - Vediamo cos'è L'acronimo "VVD" sta per Volumetric Visualization Device, sistema progettato da Lumi Industries e attualmente in attesa di brevetto. VVD è un dispositivo portatile stand-alone, che consente di esplorare un contenuto 3D. Si tratta quindi di un visualizzazione 3D "olografico" che, a differenza dei sistemi di realtà virtuale (dove è necessario l’uso di un visore), permette di vedere in modo immediato e intuitivo i modelli 3D, agevolando anche la collaborazione tra più individui eliminando la barriera del visore. "L'idea di VVD è nata dall'esigenza di avere una reale visualizzazione di un modello 3D prima di passare alla stampa 3D. Quando si progetta o si ispeziona un modello 3D, lo si fa sempre su uno schermo piatto, bidimensionale. Questo lascia spazio ad errori nel percepire le dimensioni e le proporzioni del modello. Si rischia quindi di produrlo, solo per scoprire in un secondo momento, che qualcosa non era corretto e si è sprecato tempo e denaro." Davide Marin, CEO e fondatore di Lumi Industries VVD visualizzatore volumetrico tridimensionale - Come funziona Con il software attuale, che è ancora in fase di sviluppo, è sufficiente caricare su VVD un modello 3D in formato STL, lo stesso utilizzato per la stampa 3D, che può essere il risultato di una scansione o di una modellazione 3D. Un proiettore integrato proietta i diversi strati del modello su una speciale pellicola in sincronia con il suo movimento verticale. La vibrazione della pellicola crea un effetto 3D che sfrutta il fenomeno della "persistenza della visione", una caratteristica del nostro cervello che, conservare un'immagine anche dopo che non è più visibile, ci consente di percepire un intero oggetto. L'attuale versione di VVD - si tratta ancora di un prototipo - si basa su una scheda X86 con precaricato Windows. Ha oltre 39 milioni di voxel, un volume di visualizzazione di 90x60x45 mm, connettività USB e WIFI e un display LCD da 7" e altoparlanti audio per aggiungere un ulteriore livello di informazioni sulla proiezione volumetrica. L'ingombro complessivo del dispositivo è di 36 x 20 x 24 cm. VVD visualizzatore volumetrico tridimensionale - A cosa serve VVD può trovare numerosi utilizzi all'interno di diversi ambienti: sicuramente lo sviluppo ingegneristico, la progettazione e il design del prodotto sono i settori che possono trovare immediato riscontro positivo, magari per ricontrollare un contenuto 3D e discuterlo con i colleghi o con un cliente prima della produzione, in modo da evitare ogni spreco di tempo e denaro. La condivisibilità dell'esperienza della visualizzazione rende VVD utile in molti campi diversi, come ad esempio: • Uso medico / dentale: VVD può essere utilizzato per visualizzare scansioni 3D o modelli elaborati a partire da MRI (risonanza magnetica) e CT (tomografia computerizzata) insieme ai pazienti in modo da fornire loro una spiegazione visivamente più chiara, con studenti e specializzandi, arricchendo le lezioni con immagini realmente tridimensionali di organi o parti del corpo, con i colleghi, per discutere, analizzare e ottenere valutazioni più corrette. • Educational: VVD è lo strumento perfetto per stimolare l'interesse e la curiosità degli studenti durante le lezioni utilizzando modelli 3D anziché normali immagini bidimensionali. L'interazione con l'insegnante o i compagni è stimolata dal fatto che la visualizzazione è condivisibile con più persone contemporaneamente da diversi punti di vista. • Ambito museale / mostre / marketing e comunicazione: VVD, è un singolo dispositivo che il pubblico può guardare assieme, senza bisogno di doversi dotare di singoli occhiali speciali. VVD è lo strumento perfetto per l'attenzione su un artefatto o un reperto che si vuole mettere in evidenza o un prodotto che si sta per lanciare. Mentre sullo schermo frontale di cui è dotato, è possibile aggiungere didascalie, video e descrizioni. • VVD può anche essere utilizzato per la visualizzazione di dati DEM del terreno e altre superfici, nonché per modelli di architettura in scala per esterni e interni. Link alla campagna Kickstarter.
-
Sempre, ogni anno, la Torino Mini Maker Faire presenta qualche piccola sorpresa. L'edizione 2018, oltre ad essere stata baciata dal sole, si è caratterizzata per la presenza in dimostrazione di una stampante 3D che ha riscosso molto interesse a seguito del suo lancio sul mercato, avvenuto nel mese di aprile: la nuova Ultimaker S5. In questa occasione, ho potuto toccarla con mano e ho avuto l'occasione di scambiare qualche parola con il rivenditore italiano 3D Italy, il quale renderà disponibile la Ultimaker S5 presso il proprio store di Torino. Ultimaker S5 - Caratteristiche tecniche Partendo dalla solida base delle macchine precedenti, Ultimaker ha deciso di fare parecchi passi avanti con la S5, ammiccando al segmento professionale. Ultimaker S5 è una macchina solida, grazie a una struttura in metallo racchiusa dai classici mannelli in plastica che caratterizzano le Ultimaker. Gli assi di movimentazione sono maggiorati e, a detta del produttore, consentono di avere una precisione ancora maggiore nei movimenti. Il piano di stampa è intercambiabile: sarà da usare in alluminio anodizzato per i materiali come ABS e PC, in vetro per tutti gli altri. Finalmente, è stato aggiunto un sensore di rilevamento del filo, che va a integrare il sistema di rilevamento delle bobine in utilizzo tramite tecnologia nfc. Questo significa che, sia in caso di mancata estrusione, sia in caso di errata impostazione dei materiali di stampa, la macchina darà un segnale di errore per allertare l'utente. Il diametro dei fili utilizzabili è di 2.85 mm, anche prodotti da terze parti. Per monitorare la fase di produzione anche a distanza, troviamo una piccola webcam incorporata nel volume di stampa. Infine, una bella sorpresa: lo sportellino frontale a doppia anta. A differenza della maggior parte degli sportelli che si vedono sulle stampanti 3D più economiche, quello montato sulla Ultimaker S5 è solido, con due perni di rotazione ben saldi alla struttura. Vediamo ora la scheda tecnica e, poco sotto, parleremo del nuovo blocco estrusore dotato di elettronica. Tecnologia: FDM Estrusore: blocco dotato di doppio estrusore, con sistema di movimentazione verticale degli ugelli e di rilevamento elettronico della testa di stampa Volume di stampa: X 330 x Y 240 x Z 300 mm Risoluzione: ugello da 0.25 mm -> 60-150 micron ugello da 0.4 mm -> 20 - 200 micron ugello da 0.8 mm -> 20-600 micron Precisione su XYZ: 6.9 ; 6.9 ; 2.5 micron Piano di stampa: riscaldato, in vetro e alluminio Temperatura di lavoro del piano: 20 - 140 °C Materiali supportati: PLA, ABS, Nylon, CPE, PC, TPU, PP, PVA, materiali di terze parti da 2.85 mm Temperatura di lavoro dell'estrusore: 180 - 280 °C Rumore in attività: 50 dBA Consumo: 500 W Connettività: wifi, Lan, usb Ultimaker S5 - Il blocco estrusore La maggior parte dei miglioramenti introdotti dalla Ultimaker S5 stanno nel blocco estrusore. Completamente racchiuso in un case bianco, il blocco estrusore comprende una serie di ventole di raffreddamento e due estrusori, i quali sono facilmente removibili tramite un sistema a incastro. Inoltre, ogni estrusore è stato dotato di una piccola componente di elettronica: il singolo estrusore viene quindi rilevato dalla stampante 3D e, grazie al codice identificativo, viene associato a un materiale di stampa specifico. Questo sistema di rilevamento era già stato integrato da Makerbot ormai qualche anno fa con gli Smart Extruder, dove a essere rimosso era tutto il blocco estrusore. Ultimaker, già a partire dalle Ultimaker 3, ha avuto un approccio più "tradizionale": gli estrusori sembrano ben progettati su misura e, a parte per il sistema di incastro a plug, non differiscono molto dai normali estrusori montati sui modelli precedenti. Ultimaker S5 - Considerazioni e prezzo di vendita Viste le caratteristiche tecniche e i nuovi sistemi integrati, devo dire che la macchina ha suscitato una buona impressione. I materiali di costruzione sono di qualità. Tra tutte le componenti regna il blocco estrusore, il quale sembra sia stato progettato fino al minimo dettaglio per garantire un sistema veloce e affidabile, ideale per professionisti e aziende. Ultimaker S5 è in vendita a € 5.495 + iva, disponibile sia sul sito Ultimaker e presso i rivenditori ufficiali italiani.
-
- stampanti 3d
- news
-
(and 3 più)
Taggato come:
-
Da quanto tempo non sentivamo parlare di stampa 3D a pellet? Ne parlammo già nell'ormai lontano 2014, quando uscirono i primi modelli di estrusori per filamento. Ai tempi si parlava di Filafab e Filabot, macchine ancora presenti oggi sul mercato che, una volta riempite di materiale in granuli, permettono di estrudere filamento da riutilizzare in fase di stampa 3D. Oggi, invece, sono a raccontarvi di un approccio completamente diverso all'uso di pellet per la stampa 3D: DIRECT 3D Pellet Extruder è un'estrusore a pellet che va a sostituirsi completamente al blocco estrusore delle stampanti 3D FDM, portando avanti quello che potremmo definire come una "stampa 3D diretta a pellet". DIRECT 3D Pellet Extruder - Cos'è e che vantaggi porta Il funzionamento di DIRECT 3D Pellet Extruder è semplice e per certi versi innovativo: attraverso tecnologia FDM, fonde la materia prima in forma di granuli, polvere o scaglie, stampando direttamente l'oggetto in fase di produzione. DIRECT 3D Pellet Extruder consente di utilizzare una gamma di materiali molto ampia, alcuni dei quali non compatibili con i classici estrusori a filamento. Nella gamma di materiali utilizzabili, oltre a PLA, ABS, PA, PP e PE, troviamo anche TPU, PC-ABS, PA-SGF, PA-CF, PP-SGF, PP-CF e PET, PS, materiali riciclati. Ciò consente un'apertura maggiore della stampa 3D nel campo professionale, favorendo l'uso di materiali differenti. Come in tutte le applicazioni che vedono coinvolte le plastiche in pellet, anche in questo caso troviamo benefici nei costi. Infatti, la plastica in pellet ha un costo ridotto rispetto i filamenti in bobina tradizionali. Secondo il produttore, la velocità di stampa di DIRECT 3D Pellet Extruder si allinea a quella dei normali estrusori sul mercato. DIRECT 3D Pellet Extruder - Caratteristiche tecniche Peso: 1 Kg Portata: 30 – 250 g/h Dimensione ugelli: 0.4 – 2.5 mm Temperatura massima di estrusione: 320-340 °C "E lato elettronica?", vi starete chiedendo. Il produttore afferma che DIRECT 3D Pellet Extruder risulta applicabile per elettronica e firmware alla maggior parte delle stampanti 3D presenti sul mercato e che la sua logica di funzionamento si avvicina molto a quella degli estrusori a filo conosciuti.
-
- stampanti 3d
- design
- (and 4 più)
-
La casa produttrice polacca Sinterit, con il modello Lisa, è stata una delle prime a lanciare sul mercato una stampante 3D SLS desktop, rendendo accessibile anche alle piccole aziende quella che è una delle tecnologie di stampa 3D più ricercate. A distanza di oltre un anno dal lancio i questo modello e per fare in modo che la tecnologia SLS non rappresenti più un’esclusiva delle applicazioni industriali, Sinterit sta introducendo una nuova macchina: Sinterit Lisa 2, stampante 3D SLS desktop, ideata appositamente per sostenere la creatività di ingegneri e progettisti e destinata all'uso diretto in ufficio o in laboratorio. SINTERIT LISA 2: LA NUOVA STAMPANTE 3D DESKTOP SLS Dopo circa 18 mesi di sviluppo, Sinterit Lisa 2 promette di avere prestazioni migliori rispetto al modello precedente, permettendo di ottenere stampe eccellenti a un prezzo accessibile, aunitamente alla facilità d'uso e alla possibilità di usare diversi materiali. “Nel 2014, Sinterit è stata la prima azienda a immettere sul mercato una stampante SLS in versione desktop. Grazie alle macchine desktop Sinterit, questa tecnologia risulta finalmente accessibile ad una vasta gamma di settori e può fornire a progettisti ed ingegneri possibilità illimitate. Ora, il nostro team di esperti sta per compiere un ulteriore passo in avanti. Infatti, stiamo introducendo sul mercato una macchina ancora più potente” - afferma Konrad Głowacki, cofondatore dell'azienda Sinterit. ELEVATO VOLUME DI STAMPA Sia il modello Lisa e la nuova Lisa 2 sono in grado di stampare pezzi resistenti e con geometrie molto complesse, grazie alla tecnologia SLS. Lisa 2 tuttavia, permette di stampare elementi di dimensioni maggiori, fino a una grandezza massima di quasi 32 cm in diagonale. Di seguito la tabella comparativa dei volumi di stampa per i due materiali PA12 e Flexa. Lisa 1 Lisa 2 Nylon PA12 90 x 110 x 130 mm 90 x 120 x 230 mm Flexa 110 x 130 x 150 mm 110 x 160 x 250 mm CAMERA AD AZOTO PER MATERIALI PERFORMANTI Quella che forse è la novità più grande lato hardware riguarda la camera di stampa. Per Lisa 2, infatti, la scelta è ricaduta su una camera ad azoto che, grazie alla sua speciale conformazione, permette di usare polveri come Flexa Gray e Nylon PA11. “I clienti sono soddisfatti delle nostre polveri, ma sono sempre alla ricerca di materiali sempre più performanti. Per rispondere alla crescente richiesta, abbiamo deciso di progettare una nuova macchina adatta alla sperimentazione. Grazie alla camera ad azoto possiamo creare un ambiente speciale all’interno della stampante e ampliare la lista dei materiali potenzialmente utilizzabili” afferma Michał Grzymała-Moszczyński, uno dei fondatori, nonché responsabile del reparto ricerca e sviluppo. I materiali stampabili sono i già noti Nylon PA12, per parti robuste e resistenti agli agenti chimici, nonché il Flexa back, un materiale simile al TPU e destinato ad applicazioni simil-gomma. Le nuove polveri disponibili al lancio della nuova Lisa 2 sono il Flexa grey, caratterizzato da una maggiore elasticità, dalla resistenza agli agenti chimici e alle temperature estreme e il Nylon PA11, molto resistente agli agenti chimici e alle alte temperature. SOFTWARE AVANZATO & ACCESSORI MIGLORATI Lato software, Lisa 2 arriva insieme al nuovo software Sinterit Studio 2018, creato da un team di ex-dipendenti Google, e garantisce la massima automazione e una migliore user experience. Grazie al sistema completo Sinterit, il processo di produzione è rapido e semplice. Sia il Sinterit Sandblaster che il Powder Sieve - entrambi indispensabili per pulire i pezzi prodotti e e donargli una maggiore resistenza - permettono risparmio di tempo e accelerano il flusso del lavoro. PERCHE’ UTILIZZARE LA TECNOLOGIA SLS? La tecnologia SLS rappresentava in precedenza una prerogativa delle grandi aziende, a causa dei costi proibitivi. L’avvento di stampanti 3D più economiche e adatte a realtà più piccole simboleggia senza alcun dubbio l’interruzione di questa esclusività industriale. La SLS è la tecnologia che impiega un raggio laser ad alta potenza per sinterizzare polvere di un Nylon e risulta perfetta per le applicazioni industriali poiché è in grado di: creare parti complesse, con geometrie elaborate o con elementi che devono muoversi tra di loro pur restando uniti - non è neessario generare strutture di supporto; conferire alle parti durevolezza, un’alta resistenza meccanica e un’elevata precisione dimensionale; realizzare prototipi funzionali e parti molto dettagliate (min. spessore della parete 0,04 mm dimensione del dettaglio 0,01 mm). La polvere non sinterizzata può essere riutilizzata, limitando il consumo di materiale. “È possibile riutilizzare fino al 100% della polvere, e nel caso della stampa con Sinterit, basta aggiungere il 30% di polvere fresca alla nuova stampa. Questi parametri rappresentano l'opzione più economica presente sul mercato" afferma Janne Kyttanen, attuale cliente dell'azienda. - vuoi saperne di più sulle tecnologie di stampa 3D? Leggi la nostra guida! - UNA TECNOLOGIA ADATTA A TUTTI I SETTORI L’accessibilità della tecnologia SLS che Sinterit offre in una macchina desktop e la vasta gamma di materiali, conferisce ai prototipi e ai pezzi stampati la possibilità di essere utilizzati in diversi settori come l’automotive, l’elettronica, il medicale… Il PA12 che rappresenta in questo campo il materiale più popolare, viene utilizzato soprattutto per la stampa di turbine, tubi o involucri per dispositivi elettronici, mentre il PA11 per la stampa di camme, impugnature di utensili o corrimani. ECONOMICITÀ ALLA PORTATA DI TUTTI E PER TUTTI I SETTORI Sinterit Lisa 2 è disponibile in prevendita al prezzo di € 11.990, mentre il prezzo per il Complete System (comprensivo di setacciatore, sabbiatrice e 6 Kg di materiale) è di € 13.990. Le prime consegne sono previste per Settembre 2018. E’ possibile preordinare la macchina o richiedere maggiori informazioni contattando il rivenditore autorizzato per l’Italia Manufat. Hai ancora qualche dubbio sul funzionamento della stampa 3D SLS? Cerchi maggiori informazioni sui materiali disponibili e i costi di gestione? Apri una discussione sul forum!
-
- stampanti 3d
- settori
- (and 6 più)
-
Pubblicazione comunicato stampa Arrivano con le loro scatole, le aprono e guardano il contenuto, ordinatamente disposti ci sono un paio di centina di parti, il più viti e dadi di varie dimensioni e forma. Il gioco è metterli ognuno al proprio posto e far funzionare la stampante. Anzi no! Il gioco è imparare cosa fanno, perché vanno lì e come funziona la stampante. Giovedì sera scorso StuffCube, alla biblioteca di Canegrate, ha iniziato il montaggio e l’imparaggio collettivo delle stampanti 3D. Durante l’Arduino day del 7 aprile abbiamo proposto il laboratorio di montaggio della propria stampante 3D. Abbiamo scelto quale stampante acquistare e, Amazon permettendo, i partecipanti hanno ordinato e ricevuto il kit. Nel corso di quattro incontri assembleremo le parti, impareremo il loro nome e il loro scopo, condivideremo i piccoli trucchi che l’esperienza insegna. Un poco come accade nelle botteghe artigiane. I nostri apprendisti usciranno dalla bottega di StuffCube con una stampante 3D funzionante. Ma questo potevano già farlo ordinando il kit montato. Usciranno con la conoscenza che consegue ad averla montata e compreso la funzione tar i vari pezzi. La relazione tra ognuno di questi che hanno unito uno dopo l’altro. Usciranno con l’esperienza di avere lavorato insieme risolvendo le difficoltà una dopo l’altra. Ma quali mai saranno queste? Partiamo dalle istruzioni, ci sono ma a volte non sono perfettamente aggiornate, alcuni pezzi cambiano un poco la forma pur mantenendo la funzione. Oppure il grande classico, confondere destra con sinistra o montare al contrario. Tutte cose che si fissano nella mente facendo, un poco come gli esercizi a scuola e farli assieme a un mentore che ti guida fa imparare di più. Gli incontri di StuffCube proseguono ogni mercoledì sera alle 21:00 alla biblioteca di Canegrate. Sino a metà giugno è di scena il montaggio delle stampanti. Seguirà poi la presentazione di Arianna, il robot bibliotecario giunto ormai a una solida funzionalità. Ci trovate a infostuffcube@gmail.com / www.stuffcube.wordpress.com
-
Le applicazioni della stampa 3D nel mondo del Motorsport sono svariate: si passa dall'ottimizzazione delle geometrie delle componenti meccaniche, alla produzione su misura di pezzi in metallo. Spesso però, le necessità arrivano nel momento in cui meno te le aspetti... sulla pista da corsa nel bel mezzo di una gara, per esempio. E' così che GRT Yamaha Official Team WorldSSP, attuali campioni mondiali in carica del campionato WorldSSP, insieme a MarkOne, azienda innovativa che progetta e sviluppa stampanti 3D professionali, hanno deciso di introdurre per la prima volta nel mondo del Motorsport stampanti 3D all'interno del box. Yamaha Official Team e la stampante 3D MarkOne Mark One è un'azienda che progetta e sviluppa stampanti 3D, ponendosi sul mercato con soluzioni all’avanguardia e materiali tecnici innovativi. Grazie a questa visione e a scelte aziendali indirizzate verso la ricerca e lo sviluppo, GRT Yamaha e MarkOne sono in grado di realizzare componenti real time, poi implementati sulla moto in gara, riducendo drasticamente tempi e costi di produzione. Tutto questo è reso possibile dalla presenza di una stampante 3D MarOne nei box del team motociclistico. Parliamo di nuovi distanziali poco reperibili, tappi, supporti, staffe e altre componenti che, compatibilmente coi tempi di fabbricazione e necessità, possono essere prodotte all'interno del box nei tempi richiesti. A questo, si aggiunge la possibilità di produrre geometrie complesse con materiali tecnici, come nel caso delle componenti ottimizzate per migliorare i processi di cambio gomme. Per MarkOne l’additive manufacturing, quando efficacemente studiato, ha applicazioni che vanno ben oltre lo studio prototipale, raggiungendo facilmente la produzione. Tutto ciò ha introdotto MarkOne a collaborazioni in differenti ambiti industriali, dalla fabbricazione di componenti automotive alle macchine automatiche, dal design del prodotto industriale al settore medicale ed aerospaziale grazie all'alta flessibilità delle sue macchine e dalla possibilità di realizzare soluzioni uniche. Il Team ufficiale GRT Yamaha WorldSSP vanta il corridore Mirko Giansanti, ex 125 e 250, come direttore sportivo e tecnico, e Filippo Conti come Team Manager. Con sede nel centro Italia, appena fuori Terni, la squadra ha progredito attraverso campionati nazionali ed europei negli ultimi anni prima di dedicarsi al Campionato WorldSSP nel 2016. Probabilmente, grazie alla sua nuova strumentazione, il Team GRT Yamaha WorldSSP potrà migliorare ulteriormente i propri risultati, seguendo strade che, fino a qualche mese fa, sarebbero state impensabili.
-
- stampanti 3d
- settori
-
(and 4 più)
Taggato come:
-
Arriva aria di novità da questa edizione di Technology Hub, fiera leader in Italia per le tecnologie innovative, che si terrà a Fieramilanocity dal 17 al 19 maggio. Come altre aziende del settore, WASP ha deciso di utilizzare questo palcoscenico per presentare al pubblico la nuova linea di stampanti 3D per l'argilla - WASP Linea Clay. WASP Linea Clay - Stampanti 3D dedicate a argilla e materiali ceramici "Da sempre WASP punta con decisione alla ricerca e allo sviluppo di sistemi per consentire e promuovere in tutto il mondo l’utilizzo nella stampa 3D di materiali come l’argilla, la ceramica, la porcellana. Ora l’azienda guidata da Massimo Moretti annuncia un’importante novità ... la sua nuova Linea Clay". Oltre alla presentazione di WASP Linea Clay, l'invito è quello di andare a vedere coi propri occhi stampanti 3D di diverso formato, abilitate a produrre modelli tridimensionali con diversi materiali. Caratteristica distintiva delle macchine progettate dell'azienda di Massa Lombarda è proprio quella della versatilità: sostituendo il blocco estrusore è possibile passare dalla stampa 3D di polimeri (ABS, HIPS, PETG, PA carbonio) a quella di argilla, utilizzando sempre la stessa macchina come supporto meccanico. Inoltre, i più attenti potranno analizzare quelli che sono stati dei miglioramenti a livello di carrelli di movimentazione, firmware, caricamento dei serbatoi. Insieme a WASP Linea Clay, sarà esposta l'intera famiglia delle famose stampanti 3D delta. Tra queste, DeltaWASP 3MT Industrial, utilizzabile sia a filamento che a granuli, progettata appositamente per realizzare oggetti di grandi dimensioni come statue, complementi d'arredo, casse acustiche e scenografie per spettacoli teatrali come già avvenuto per l’opera Fra Diavolo presentata al Teatro dell’Opera di Roma e al Teatro Massimo di Palermo. WASP vi aspetta allo stand E20 del Technology Hub di Milano. Nell’occasione verrà organizzata la premiazione dell’architetto Marco Parnasi, vincitore del 3D Printing Light Contest con il suo progetto Aureal Twist.
-
- stampanti 3d
- eventi
-
(and 6 più)
Taggato come:
-
In occasione di Technology Hub, l’evento professionale sulle tecnologie innovative in programma dal 17 al 19 maggio 2018 a Fieramilanocity, saranno presentate diverse novità in ambito stampa 3D. Tra le aziene espositrici, Sharebot svelerà al pubblico una nuova stampante 3D, completamente rivisitata rispetto ai modelli già messi in commercio dalla casa madre di Nibionno. Nuova stampante 3D Sharebot - quale tecnologia? "Presenteremo per la prima volta al pubblico la nostra rete capillare di 3D Store che, avendo raggiunto il traguardo di 9 punti vendita disseminati sul territorio italiano, è ufficialmente diventata la rete proprietaria con più negozi inerente alla stampa 3D e alle tecnologie additive" si legge nel comunicato stampa arrivato qualche giorno fa nella nostra casella email. L'obiettivo di Sharebot sarà quello di dare risalto ai singoli progetti presentati dagli Store, ognuno dei quali strettamente legato a uno specifico settore merceologico. "La politica di Sharebot mira così a evolversi mettendo in evidenza, oltre al prodotto, i campi applicativi che possono trarre grande vantaggio da Additive Manufacturing e prototipazione rapida e il know-how del personale qualificato degli Store, in grado di fornire service, assistenza, formazione e consulenza tecnica". A completamento di quella che sicuramente sarà una bella vetrina composta da pezzi stampati in 3D d'interesse, troveremo la presentazione dell'ultima macchina progettata dall'azienda. Seppure ancora non si abbiano dettagli tecnici, neanche a riguardo della tecnologia su cui si baserà questa nuova stampante 3D - FDM? DLP? - Sharebot si sbilancia, definendola come "rivoluzionaria". Dotata di grande precisione e velocità di esecuzione, insieme alla qualità della finitura superficiale, sembra che avremo l'opportunità di mettere gli occhi su qualcosa di migliorativo. Indirizzata a un livello di utenza professionale, la nuova stampante 3D sarà dotata di accortezze tecniche che la renderanno comoda e veloce da usare nell'ambito dell'industria, probabilmente grazie a materiali e profili già preparati dalla casa madre (come di consuetudine per Sharebot). Questa macchina sarà in grado di "concretizzare i progetti e realizzare i sogni delle PMI e delle aziende tutte". Parliamo quindi una stampante FDM? Oppure ci troveremo davanti a un modello DLP? Non ci resta che attendere ancora qualche giorno, magari sperando di ricevere - o captare per vie traverse - qualche informazione in più.
-
- stampanti 3d
- eventi
-
(and 3 più)
Taggato come:
-
Pubblicazione comunicato stampa Kentstrapper presenta oggi la stampante 3D Mavis, ultimo modello realizzato dalla casa produttrice fiorentina, in cui si fondono insieme tecnologia avanzata e semplicità di utilizzo. Abbiamo scelto per la stampante 3D MAVIS un area di lavoro 400x400x700 mm al fine di permettere la realizzazione di prototipi di grandi dimensioni senza la necessità di scalarli o sezionarli Tutte queste caratteristiche rendono il nuovo prodotto in linea con le prestazioni e l’attenzione al design del brand Kentstrapper. CALIBRAZIONE AUTOMATICA Giusto il tempo di iniziare La parte più complicata nell’utilizzo di una stampante 3D risiede nella procedura di calibrazione del piatto di stampa. Abbiamo cercato la soluzione a questo problema e abbiamo dotato la stampante 3D Mavis di un sistema automatizzato di calibrazione. Appena la accederai sarai in grado di stampare senza dover effettuare nessuna procedura di calibrazione SMART GUI Una vista dinamica La nuova interfaccia è dinamica dove icone colorate con raffigurazioni permettono all’utente di accedere ai comandi in modo semplice e veloce. Nessuna manopola, nessun click, il display touch screen da 5 pollici permetterà di gestire tutto con il semplice tocco delle dita. La stampante 3D MAVIS è in grado di capire se il filamento è terminato e di salvare il processo di stampa per poi essere riavviato, una volta aver ricaricato il filamento. http://www.stampa3d-forum.it/wp-content/uploads/2017/04/Mavis-Kentstrapper-2.jpg PHOENIX SYSTEM Interrompi. Arresta. Riprendi quando vuoi. L’interruzione di corrente non causerà mai più il fallimento della vostra stampa. La stampante 3D MAVIS è in grado di capire se viene privata dell’alimentazione e di salvare il processo di stampa. Sul display della stampante apparirà un messaggio che notifica l’assenza di alimentazione e non appena l’alimentazione ritornerà la stampante 3D ripartirà da dove si era interrotta. Questo sistema permette anche di gestire il processo di stampa, può essere messo in pausa o arrestato per poi riprenderlo in un secondo momento. INGRESSO USB KEY Un unica chiave d’acesso alla stampa. Ingresso Usb per il caricamento dei file di stampa. WI-FI Controllo remoto della stampante tramite Wi-fi. Possibilità di controllare la stampante tramite il Wi-fi.
- 23 commenti
-
- stampanti 3d
- settori
-
(and 7 più)
Taggato come:
-
Pubblicazione comunicato stampa Milano, 1 Marzo 2017 - ACTLAB - Politecnico di Milano presenta in anteprima al Made Expo 2017 Trabeculae Pavilion, un’architettura sperimentale che coniuga stampa 3D e ricerca biomimetica. Dal 8 al 11 Marzo, all’interno dell’area BSmart!, nel padiglione 10 della Fiera di Milano-Rho verrà presentato un primo prototipo di costruzione leggera che dimostra le potenzialità rivoluzionarie delle innovazioni nel campo del design computazionale e della stampa 3D per il mondo delle costruzioni. Questo progetto è la sintesi di una ricerca incentrata sull’uso di tecniche innovative di manifattura additiva nelle costruzioni e su come queste possano fornire nuove soluzioni ai problemi della nostra contemporaneità. La stampa 3D è utilizzata come metodo evoluto per affrontare il problema della scarsità di risorse. “Gli ultimi decenni hanno visto una crescita esponenziale nella domanda di materie prime a causa della rapida industrializzazione di economie emergenti e dell’alto consumo di materiali. Questa ricerca guarda ai modelli biologici e alle opportunità offerte da nuove tecnologie di produzione additiva per trovare soluzioni sostenibili nell’uso dei materiali. Il nostro obiettivo è studiare un nuovo tipo di architettura non-standard: evoluta, efficiente e sostenibile”, affermano Roberto Naboni, architetto e ricercatore al Politecnico di Milano e Ingrid Paoletti, Professore Associato in Tecnologia delle Costruzioni al Politecnico di Milano. http://www.stampa3d-forum.it/wp-content/uploads/2017/03/ACTLAB-Trabeculae-padiglione-stampa-3d-3.jpg Il padiglione è un prototipo dimostrativo a grande scala completamente stampato in 3D con un biopolimero ad alte prestazioni sviluppato assieme al partner industriale Filoalfa, che ha permesso di elevare la stampa a deposizione fusa (FDM) ad applicazioni strutturali. La produzione dei componenti a geometria complessa è realizzata con una printing farm di stampanti Wasp, in grado di assicurare una produzione continuativa e di precisione, anche attraverso l’utilizzo di un estrusore sperimentale che permette di fabbricare strutture resistenti dimezzando i tempi di produzione. Una sinergia di progetto, materiali e tecnologie che hanno permesso di concepire un’innovativa tecnica di costruzione additiva, in cui l’organizzazione materiale di forme architettoniche complesse viene definita in modo adattivo. “Abbiamo guardato alla Natura e a come questa costruisca forme leggere e resistenti al tempo stesso per minimizzare l’uso di risorse materiali. Studiando la struttura interna delle ossa, abbiamo creato degli algoritmi che ci permettono di ottenere strutture cellulari tridimensionali con la precisione dei decimi di millimetro per realizzare architetture complesse, sempre diverse e ad alta efficienza”. http://www.stampa3d-forum.it/wp-content/uploads/2017/03/ACTLAB-Trabeculae-padiglione-stampa-3d.jpg Al Made Expo verrà presentata la ricerca raccontando i vari aspetti interdisciplinari che la caratterizzano, spaziando dalla progettazione computazionale alla biomimetica, dalla manifattura innovativa dell'ingegnerizzazione dei materiali. Verrà esposto un prototipo di involucro leggero alla grande scala, accompagnato da un centro di produzione con stampanti 3D che produrrà in diretta i componenti che andranno a costituire il Trabeculae Pavilion, la cui costruzione verrà completata a fine fiera presso i laboratori del Politecnico di Milano. ACTLAB - Dipartimento ABC, POLITECNICO DI MILANO ACTLAB (Laboratorio di Architettura, Computazione e Tecnologia) è un’unità di ricerca fondata da Ingrid Paoletti e Roberto Naboni nel 2014 con l’obiettivo di esplorare l’ambito di intersezione dell’architettura con tecniche computazionali, tecnologie emergenti e la scienza dei materiali. ACTLAB fa parte del Dipartimento di Architettura, Ingegneria delle Costruzioni e Ambiente Costruito (ABC) del Politecnico di Milano. CREDITI DI PROGETTO Trabeculae Pavilion è un progetto promosso da ACTLAB, Dipartimento ABC - Politecnico di Milano Coordinamento Scientifico: Roberto Naboni, Ingrid Paoletti Sviluppo Scientifico: Roberto Naboni (Project Leader ), Anja Kunić (Computational Design), Luca Breseghello (Computational Design), Francesco Martelli (Analisi Strutturale). In collaborazione con ITKE - University of Stuttgart: Valentin Koslowski (Analisi Strutturale e Prove Materiali), Jan Knippers Collaboratori: Rahul Sehgal, Maia Zheliazkova, Francesco Pasi, Erik Zanetti, Bilyana Savova.
-
- settori
- architettura
-
(and 4 più)
Taggato come:
-
Pubblicazione comunicato stampa Dal 23 al 25 marzo saranno presentate in anteprima all’edizione 2017 del Mecspe di Parma le innovazioni in casa WASP. Fiera di riferimento per l'industria manifatturiera, il Mecspe offre una panoramica completa su materiali, macchine e tecnologie innovative. WASP sceglie questa occasione per presentare cinque importanti novità. La nuova linea di stampanti 3D Industrial DeltaWASP 4070 Industrial http://www.stampa3d-forum.it/wp-content/uploads/2017/03/4070industrial.59.png Rivisitazione del modello classico, è realizzata interamente in metallo, con camera riscaldata a ventilazione forzata, coibentata per l’isolamento termico e dei rumori. Ha un sistema di filtraggio fumi integrato e nuove meccaniche progettate per lavorare in camera calda. Permette la stampa di materiali tecnici stampabili solo in camera calda. DeltaWASP 3MT Industrial http://www.stampa3d-forum.it/wp-content/uploads/2017/03/3mtchiusarender.38.png E’ l’interpretazione industriale della DeltaWASP 3MT, con camera coibentata per l’isolamento termico e acustico, struttura completamente chiusa e in metallo che elimina ogni vibrazione in fase di stampa. Permette stampe di qualità superficiale comparabili a quelle delle piccole stampanti ma con area di stampa elevata al cubo. Può montare un estrusore a granuli per stampare oggetti in grandi dimensioni con ugelli fino a 3mm. Per il filamento può essere equipaggiata con estrusori da 0,4; 0,7; 1,2mm. Nuova DeltaWASP 2040 Turbo2 http://www.stampa3d-forum.it/wp-content/uploads/2017/03/2040I.951.png Versione rivista e implementata della classica DeltaWASP 2040 Turbo, per una stampante 3D ancora più precisa e affidabile. Monta una nuova scheda 32bit integrata di classe industriale. Si fornisce con un sistema di alimentazione che può supportare 2 estrusori ad alta potenza. La Turbo 2 presenta un nuovo sistema di scorrimento dei carrelli che ne incrementa la velocità e la precisione. La camera è stata meglio coibentata per poter raggiungere temperature adatte a stampare materiali tecnici ed è dotata di un sistema di raffreddamento dei motori e delle schede e di una cinematica per le alte temperature. Viene presentata con il doppio estrusore opzionale. Non solo stampanti 3D, ma anche nuovi blocchi estrusori http://www.stampa3d-forum.it/wp-content/uploads/2017/03/spitfire.png WASP Spitfire è un blocco estrusore pensato per l'alta precisione a velocità elevate. Può macinare fino a 30 metri l'ora di filamento. Lo Zen Extruder è un blocco estrusore con sistema di pulizia e ugelli dotati di un sistema di movimento che favoriscono la buona riuscita di stampa a più materiali.http://www.stampa3d-forum.it/wp-content/uploads/2017/03/spitfire-3.jpghttp://www.stampa3d-forum.it/wp-content/uploads/2017/03/spitfire-2.jpg
- 2 commenti
-
- stampanti 3d
- eventi
-
(and 9 più)
Taggato come:
-
"25 micron reali, motori potenziati, nuovo estrusore in acciaio INOX, maggiore versatilità dei materiali, ideale sia per la prototipazione sia per prodotti finiti di alta qualità." Sono queste le prime righe che leggiamo nell'ultimo comunicato stampa ricevuto da Roboze, nota azienda italiana produttrice della stampante 3D Roboze One. http://www.stampa3d-forum.it/wp-content/uploads/2017/04/Roboze-One-Lateral-1024x1024.jpg Roboze One è una stampante 3D professionale e ad alte prestazioni, ancora una volta potenziata e revisionata con l'obiettivo di posizionarsi fra i top di gamma all’interno delle PMI. Nel settore, Roboze è conosciuta per una grande attenzione alle precisioni meccaniche e per la sua offerta di materiali performanti come il PEEK e il PEI. Roboze One - Le novità Diversi sono gli aggiornamenti che Roboze ha effettuato sul suo modello di punta. In primo luogo vi segnalo il miglioramento delle tolleranze nei movimenti. Grazie al brevetto Beltless System, Roboze ha da sempre potuto offrire un sistema a tolleranze reali che, con questi ultimi miglioramenti, raggiungono i 25 micron. http://www.stampa3d-forum.it/wp-content/uploads/2017/04/Roboze-One-Nylon-6-1024x768.jpg http://www.stampa3d-forum.it/wp-content/uploads/2017/04/Roboze-One-PC_ABS-1024x768.jpg http://www.stampa3d-forum.it/wp-content/uploads/2017/04/Roboze-One-Nylon12-1024x768.jpg Il nuovo estrusore montato su Roboze One è stato progettato e viene prodotto dal team Roboze. Completamente in INOX, raggiunge 300°C allargando l’offerta di stampa dei tecno-polimeri stampabili. Oltre quindi ai materiali compatibili con il vecchio modello, ULTRA, STRONG, FLEX e FUNCTIONAL, fra le nuove possibilità si possono trovare CARBON PA, polimero ingegnerizzato con base poliammide rinforzata con 20% di fibra di carbonio; Nylon 6, poliammide ad alta resistenza meccanica, utilizzato per realizzare componenti nel settore metalmeccanico; ASA, tecno-polimero altamente resistente ad agenti atmosferici, raggi UV, ingiallimento e fenomeni di aging, caratteristiche che lo rendono adatto per componenti automobilistiche e applicazioni outdoor; PC-ABS, che miscela delle proprietà meccaniche del PC e della elevata lavorabilità del ABS, che rendono le componenti stampate non solo definite in modo eccezionale ma con anche un’ottima finitura superficiale; ABS-HD che combina le proprietà meccaniche dell’ABS con un forte livello di superficialità, utile per le operazioni di post-produzione. http://www.stampa3d-forum.it/wp-content/uploads/2017/04/Roboze-One-Extruder5-1024x768.jpg La nuova soluzione Roboze One, inoltre, integra uno schermo touch screen da 3,5 inch a colori, motori stepper da 24V con divisione dell’angolo fino a 128 step, tasti e sensori di emergenza, un sistema di ventilazione potenziato che garantisce una buona lavorabilità con il minimo rumore, ingresso scheda SD esterno e attacco USB. Tirando le somme, risulta essere fino a otto volte più precisa e con meno vibrazioni, con conseguente riduzione del rumore macchina. La nuova Roboze One sarà mostrata al pubblico per la prima volta durante il Rapid + TCT show allo stand 850, che si terrà a Pittsburg dall’8-11 Maggio, confermando anche le intenzioni del gruppo di aprirsi al mercato Americano.
-
- stampanti 3d
- news
-
(and 1 più)
Taggato come:
-
Il settore dentale è sempre stato uno dei più ricettivi nei confronti della stampa 3D, riuscendo a convertire processi manuali in sistemi digitali avanzati. Il conseguente miglioramento delle prestazioni e della qualità degli oggetti prodotti non ha fatto altro che confermare questa tendenza, spingendo le grandi multinazionali dell'additive manufacturing a migliorare ulteriormente le proprie macchine in termini di produzione, velocità e precisione, dimostrandosi sempre più competitive nel settore. Stratasys per la stampa 3D dentale - Stratasys J700 Dental Presentata in anteprima al 37th International Dental Show, la nuova Stratasys J700 Dental è stata progettata per poter sostenere una produzione di 400 stampi per allineatori trasparenti al giorno. Il materiale proposto per tale funzione è chiamato VeroDent™, materiale ottimizzato per una produzione veloce e accurata, che garantisca una fase di post-produzione più ridotta possibile. La tecnologia utilizzata da questa macchina è la PolyJet, che permette di ottenere superfici lisce e dettagli accurati con una risoluzione degli strati di 16 micron e un livello di precisione fino a 0,1 mm - questi dati tecnici sono indicativi per la tecnologia PolyJet di Stratasys e non riguardano in modo specifico questa nuova stampante 3D, di cui non abbiamo ulteriori specifiche tecniche . Ogni sessione di stampa permette la fabbricazione di più allineatori, anche differenti tra loro, ottimizzando i tempi di produzione. http://www.stampa3d-forum.it/wp-content/uploads/2017/03/Stratasys-J700-stampa-3D-dentale-01.jpg Come si evince da queste prime caratteristiche tecniche, Stratasys J700 Dental è stata progettata per quei laboratori di ortodonzia che necessitano di alte prestazioni nella fabbricazione di allineatori trasparenti. Con i maggiori volumi di produzione del segmento, l'obiettivo è quello di soddisfare le richieste delle più grandi produzioni, mantenendo inalterata la qualità dei risultati. Grandi passi avanti sono stati fatti nei confronti della semplificazione dell'intero sistema di produzione e pulizia, in modo da ridurre la necessità di riservarne l'utilizzo a utilizzatori esperti. Attraverso GrabCAD Print, software proprietario di Stratasys, è possibile gestire i modelli tridimensionali tramite parametri di base e avanzati. Il software è stato aggiornato in modo da poter dare agli operatori consigli durante il workflow di preparazione dei pezzi, fungendo da assistente anche nel processo di slicing e consigliando aggiustamenti prima di iniziare la fase di stampa. La nuova Stratasys J700 Dental sarà disponibile verso fine 2017 e presentata al pubblico in anteprima all'International Dental Show di Colonia.
-
- stampanti 3d
- settori
-
(and 4 più)
Taggato come:
-
Pubblicazione comunicato stampa Milano, 16 febbraio 2017 - Stampare in 3D oggetti metallici e ceramici sarà presto possibile grazie al nuovo dispositivo brevettato dal Politecnico di Milano, senza fondere il materiale! Il prototipo costruito e brevettato dal Politecnico, chiamato Hephæstus, è una evoluzione delle tradizionali stampanti 3D di tipo FDM - Fused Deposition Modeling, molto economiche e molto popolari per la stampa di oggetti in plastica. L’innovativa stampante è in grado di produrre oggetti metallici o in ceramica avanzata di piccole dimensioni con la stessa velocità di deposizione di una FDM convenzionale. Il dispositivo brevettato è costituito da un sistema di iniezione e da un robot a macchina cinematica parallela a cinque gradi di libertà. http://www.stampa3d-forum.it/wp-content/uploads/2017/02/prototipo.jpg L’estrusore viene mantenuto in posizione fissa, ad asse verticale, mentre è in movimento la tavola porta-pezzo, basata su una struttura ibrida caratterizzata da due meccanismi a cinematica parallela posti in serie. Il primo ha tre gradi di libertà traslazionali, mentre il secondo, denominato “polso sferico agile” è un manipolatore a due gradi di libertà rotazionali. I due manipolatori sono in grado di lavorare in modo coordinato o indipendente. I materiali caricati (detti feedstock) sono polveri metalliche o ceramiche, in granuli o pellets, ad alta percentuale di metallo, miscelate con un legante polimerico (detto binder), la cui quantità deve essere ottimizzata perché il procedimento abbia successo. Dopo la deposizione, il materiale viene decerato e sinterizzato con dei trattamenti termici, fino a raggiungere lo stato solido, compatto, omogeneo e privo di porosità residua, se non quella tipica di tutti i processi FDM.
-
- stampanti 3d
- settori
-
(and 7 più)
Taggato come:
-
pubblicazione comunicato stampa L'evento MECPE di quest'anno al Quartiere Fieristico di Parma (23-25 marzo), vedrà il debutto italiano della Serie F123 di stampanti 3D lanciata di recente da Stratasys. Completamente compatibili con GrabCAD Print, i sistemi di prototipazione professionale tutto-in-uno forniscono un flusso di lavoro completo, dal progetto alla stampa, dalla verifica concettuale iniziale, alla convalida del progetto, ai test delle prestazioni funzionali. La Serie F123 offre a progettisti e ingegneri maggiore creatività, conferma del progetto accelerata, materiali studiati e alta precisione. La scelta ideale per prototipi economici e rapidi per i gruppi di lavoro. http://www.stampa3d-forum.it/wp-content/uploads/2017/03/Stratasys-New-F123-Series-1024x683-1024x683.jpg Chi, invece, desidera prototipi e parti caratterizzati da un realismo ineguagliato, potranno vedere all'opera l'esclusiva stampante 3D J750 policromatica e multi-materiale di Stratasys. La capacità di produrre parti in multi-materiale e in tutte le sfumature di colore in una sola stampa, consente ai progettisti di ridurre il ciclo di progettazione rimuovendo diverse fasi del processo di prototipazione, ad esempio assemblaggio e post-elaborazione. http://www.stampa3d-forum.it/wp-content/uploads/2017/03/J750_AngleRight_Open.jpg Produzione di parti in filamenti caricanti in fibra di carbonio con dimostrazioni dal vivo di stampa 3D all'interno dello stand Stratasys evidenzierà il risparmio in termini di tempo e costi tra il 75% e il 90% derivati dalla produzione di parti e attrezzature con filamenti caricati con fibra di carbonio, tramite dimostrazioni dal vivo della stampante 3D Fortus 450 all'interno dello stand. Visita imperdibile per chi opera nel campo automobilistico e aerospaziale. La fabbrica del futuro – Industria 4.0 Stratasys collaborerà anche all'area “Digital Factory”. I visitatori potranno osservare da vicino il flusso di lavoro completo, dalla progettazione del prodotto alla realizzazione, evidenziando il ruolo importante che la stampa 3D svolge nell'Industria 4.0. Inoltre, Andreas Langfeld, EMEA Sales Vice Presidente di Stratasys, fornirà una presentazione approfondita, dal titolo “The Future of 3D Printing: Insights from a Market Leader” (Il futuro della Stampa 3D: analisi di un leader di mercato) giovedì 23 alle 13:00 presso la Sala Convegni Fabbricazione additiva (Padiglione 6, stand L26). Ricordiamo, per finire, che Giuseppe Cilia, Italy Sales Manager di Stratasys, parteciperà alla Tavola Rotonda “Qualità e Controlli nella produzione additiva e le sue applicazioni”, in collaborazione con l’Ordine degli ingegneri di Parma. La tavola rotonda si terrà venerdì 24 marzo dalle ore 15:30 alle ore 17:00 nella sala convegni additive manufacturing del padiglione 6. “L'evento MECSPE rappresenta la piattaforma ideale per mostrare le soluzioni di stampa 3D più recenti al mercato italiano, tra cui l'anteprima della nostra serie F123, che combina semplicità e prestazioni”, sostiene Giuseppe Cilia, responsabile vendite per l'Italia di Stratasys. “Incoraggiamo i visitatori a esplorare le modalità di ottimizzazione del processo di produzione riducendo al contempo i costi, grazie all'esclusiva gamma di stampanti 3D per la prototipazione e la produzione”. Troverete Stratasys all'interno del padiglione 6, stand J25, presso Fiere di Parma da 23 al 25 marzo.
-
Presentato in anteprima assoluta all'ultimo TCT Show, il modello Admaflex 130 ha segnato un importante passo avanti per uno di quei segmenti di mercato poco considerati dalla maggior parte degli operatori del settore, quello della stampa 3D in ceramica. Nata dalla collaborazione tra Formatec Ceramics e l'Energy Research Centre the Netherlands (ECN), la stampante 3D professionale Admaflex 130 offre la possibilità di stampare oggetti in ceramica ad alta densità. Commercializzata da Admatec, la sua progettazione iniziò nel 2013, arrivando nel 2014 a essere una macchina pronta per essere testata e ottimizzata, superando più di 5.000 ore di stampa e una lunga serie di test. http://www.stampa3d-forum.it/wp-content/uploads/2017/03/Admatec-stampa-3d-ceramica-02-1024x683.jpg Stampa 3D ceramica - I materiali Basata su una tecnologia protetta da brevetto, Admaflex 130 permette di stampare in 3D materie ceramiche in modo pulito e stabile, includendo tra i materiali utilizzabili l'ossido di zirconio (usato in odontoiatria), l'ossido di alluminio (dotato di estrema resistenza a corrosione e usura) e la silice fusa, chiamata anche "vetro di silice". I target dell'azienda olandese sono i settori medicale, dentale e della gioielleria, proprio quelli dove la presenza di materiali non a base di polimeri e dotati di caratteristiche particolari può fare realmente la differenza. In generale, possiamo dire che i materiali ceramici sono dotati di grande resistenza all'usura, limitano la propagazione delle fratture, resistono ad alte temperature, hanno buone proprietà di scorrimento, presentano un'ottimo isolamento elettrico, alta resistenza meccanica, sono bioinerti e, ancora, compatibili con prodotti alimentari. http://www.stampa3d-forum.it/wp-content/uploads/2017/03/Admatec-stampa-3d-ceramica-04.jpg Detto questo, non è necessario essere esperti materiali per convincersi che, quando metalli e plastiche falliscono a causa di alte temperature, azione di acidi, ecc, le ceramiche possono effettivamente ricoprire un ruolo importante nel mondo della stampa 3D professionale. Stampa 3D ceramica - La tecnologia La tecnologia integrata da Admatec consiste in una tecnica DLP (Direct Light Printing) che lavora un materiale fotosensibile composto da un mix di resina e polveri ceramiche. Procedendo strato su strato, l'oggetto viene poi sinterizzato, con l'obiettivo di rendere il componente abbastanza resistente per essere lucidato, sabbiato e assemblato. http://www.stampa3d-forum.it/wp-content/uploads/2017/03/Admatec-stampa-3d-ceramica-05.jpg Admatec sta portando avanti progetti di ricerca e sviluppo legati alla stampa 3D di metalli, cercando di utilizzare la stessa tecnologia proposta nella Admaflex 130. Riuscire in questa impresa significherebbe portare sul mercato un sistema più economico rispetto a quelli attuali anche se, probabilmente, più limitato dal punto di vista delle capacità tecniche degli oggetti realizzati. Insomma, non ci resta che attendere per vedere cosa Admatec riuscirà a produrre.
- 4 commenti
-
- stampanti 3d
- materiali
-
(and 3 più)
Taggato come:
-
Usare la tecnologia FDM per stampare materiali tecnici non è mai banale. Spesso si rischia di scontrarsi con problemi di hardware e componenti non idonee a soddisfare le richieste più spinte. Per questo motivo AON3D ha elaborato una stampante 3D in grado di stampare due materiali molto richiesti nel mondo professionale: ULTEM e PEEK. AON-M, la macchina professionale per ULTEM e PEEK AON-M è la stampante 3D idonea a soddisfare le richieste più elaborate. Il blocco estrusore raggiunge temperature elevate in modo da garantire l'estrusione di PEEK e Ultem, arrivando ai 380-400°C richiesti da questo tipo di materiali. A differenza dei classici blocchi estrusori da pochi soldi, perdiamo completamente il tubo in PTFE, il quale non può resistere a queste temperature, e al suo posto troviamo solo componenti in metallo. Inoltre, AON-M è dotata di due ugelli, offrendo maggiori libertà nell'uso di più materiali nella stessa stampa. http://www.stampa3d-forum.it/wp-content/uploads/2017/02/Untitled-3.jpg Con una temperatura massima raggiungibile dall'estrusore pari a 450 °C, un piano di stampa che raggiunge i 150 °C e la camera riscaldata fino a 70 °C, AON-M si attesta tra le stampanti 3D più performanti dell'anno. Il volume di stampa è di 454 x 454 x H 640 mm. La grande novità di AON-M? Il raffreddamento ad acqua Avete capito bene, ma nel dubbio torno a dirvelo: raffreddamento ad acqua. Gli estrusori sono quindi stati progettati fino al minimo dettaglio, con l'obiettivo di garantire una gestione maniacale dei dettagli con un consumo di 1200 W e un costo di mercato vicino a 15.000 €. http://www.stampa3d-forum.it/wp-content/uploads/2017/02/AON-M-INDUSTRIAL-PROFESSIONAL-3D-PRINTER-3.jpg
-
- stampanti 3d
- settori
-
(and 8 più)
Taggato come:
-
Grazie alla precisione raggiungibile nella creazione dei pezzi, la stampa 3D a sinterizzazione laser - SLS - continua ad essere una delle tecnologie più apprezzate nel mondo della manifattura additiva. Le sue applicazioni trovano spazio più che altro nel mondo professionale e industriale, sia a causa dei costi della tecnologia, che all'utilizzo di materiali molto più tecnici rispetto a quelli impiegati in altri metodi di stampa 3D. In questo ambito, uno dei materiali più utilizzati è il Poliammide 11, un materiale dotato di capacità tecniche notevoli che lo differenziano dai suoi simili. Poliammide 11 - Cos'è e le caratteristiche tecniche Chiamato anche come Nylon 11, il Poliammide 11 (PA 11) è un materiale conosciuto nel mondo dei polimeri dal 1947, anno in cui è stato lanciato sul mercato come alternativa al Poliammide 6.6, composto chimico utilizzato più che altro nel settore tessile. Le sue proprietà, molto simili a quelle del Poliammide 12 (PA 12), si differenziano essenzialmente grazie alla presenza di 11 atomi di carbonio nella catena polimerica che lo costituisce. Semplificando, possiamo dire che, grazie a questa composizione chimica, il Poliammide 11 possiede una una struttura cristallina diversa da quella del Poliammide 12, superiore in termini di resistenza meccanica, chimica e termica, oltre che nella stabilità dimensionale. Il Poliammide 11 è infatti un materiale isotropo, ossia un materiale che presenta le stesse proprietà in tutte le direzioni. http://www.stampa3d-forum.it/wp-content/uploads/2017/02/black-nylon-top-4.jpg Vantaggi del Poliammide 11 nella stampa 3D a sinterizzazione laser Resistenza agli impatti A basse temperature, i Poliammidi 12, 6 e 6.6 presentano un crollo della resistenza agli impatti, cosa che non accade al Poliammide 11, nel quale rimane pressoché invariata al variare della temperatura. Rottura a trazione Grazie alla struttura cristallina, le sue proprietà a tensione e a rottura a trazione, specialmente sull'asse Z, direzione più critica sui pezzi stampati in 3D a causa della possibilità di distaccamento tra i layer. Performance all'affaticamento Le performance all'affaticamento del Poliammide 11 sono fino al 60% migliori del Poliammide 12. Da notare, è che questa caratteristica rimane anche anche sull'asse Z. Memoria elastica Il Poliammide 11 possiede un'elevata memoria elastica, che permette al materiale di tornare alla situazione originaria anche in seguito a una distorsione del 20%. Nel Poliammide 12, questo dato scende a 5,6%. Derivazione da fonti 100% rinnovabili Essendo un derivato dell'olio di ricino, la produzione del Poliammide 11 presenta una riduzione del 41% nelle emissioni di CO2 e del 44% per le energie fossili in confronto al Poliammide 12, il quale deriva essenzialmente da combustibili fossili. Chiaramente, pur avendo molte caratteristiche positive, anche il Poliammide 11 possiede alcune limitazioni. In particolare, è necessario segnalare che non è idoneo per la produzione di oggetti che dovranno andare a contatto con cibi e bevande, non è riciclabile (anche se derivato al 100% da fonti rinnovabili) e non è a tenuta d'acqua. http://www.stampa3d-forum.it/wp-content/uploads/2017/02/black-nylon-top-3.jpg Seppure i polimeri siano da sempre prediletti nelle tecnologie additive, l'uso del Poliammide 11 ha permesso di ampliarne ulteriormente l'utilizzo in settori come quelli aerospaziale, automobilistico e medicale, presentandosi come un materiale versatile e adatto a impieghi disparati. Nell'industria d'oggi, questo viene anche adoperato come base per l'aggiunta di ulteriori componenti come fibra di carbonio, ritardanti di combustione e fibre di vetro.
-
- materiali
- ingegneria
-
(and 4 più)
Taggato come:
-
UniBo Motorsport è il Team di Formula SAE dell’Alma Mater Studiorum – Università di Bologna, nato nel 2009 dalla passione di un gruppo di studenti della Facoltà d’Ingegneria, con l’obbiettivo di progettare, costruire, assemblare e mettere in pista un’auto da corsa di tipo formula. Nel corso degli anni il Team ha sempre avuto un occhio di riguardo per le nuove tecnologie offerte dal mercato e, come potrete facilmente immaginare, una di queste è la stampa 3D. A partire dall’inizio della stagione 2017 il parco macchine a disposizione dei progettisti di UniBo Motorsport è stato ampliato con l'acquisto di una stampante 3D Mark One, modello One. Una vera e propria novità per il Team, grazie alla quale è stato possibile raggiungere nuovi obiettivi e ottenere numerosi vantaggi: maggiori libertà durante la progettazione; possibilità di creare pezzi singoli, unici e personalizzati, garantendo comunque costi contenuti; opportunità di realizzare parti complesse, difficilmente ottenibili mediante altri processi. Velocità, una parola che accomuna la stampa 3D e il motorsport Quello che vorrei raccontarvi è un particolare aneddoto successo ai ragazzi di UniBo Motorsport che sottolinea come, grazie alla stampa 3D, la rapidità nello sviluppo e la gestione delle modifiche del progetto, sia stato possibile risolvere una problematica che avrebbe compromesso tutte le prove libere previste per il periodo invernale dal gruppo sportivo automobilistico. Verso fine ottobre, a termine della seconda giornata di test invernali, la monoposto di UniBo Motorsport ha subito un problema inatteso ad uno dei semiassi. Dopo un'attenta analisi svolta in officina, si è realizzato che una delle componenti interne era danneggiata, compromettendo il corretto funzionamento dell'intero semiasse. Come da prassi, il primo pensiero del gruppo è stato quello di chiedere un pezzo di ricambio attraverso i canali classici di rifornimento componenti, ma, ottenute le risposte dai fornitori, il pezzo sarebbe arrivato dopo diverse settimane, rendendo impossibile il completamento delle due sessioni di test previste nei giorni successivi l'accaduto. http://www.stampa3d-forum.it/wp-content/uploads/2017/01/UniBo-Motorsport5-1024x772.jpg Ricevuta la brutta notizia, il pensiero dei tecnici del Team si è quindi spostato alla ricerca di un modo alternativo per poter ottenere nei tempi più brevi possibili una copia del pezzo compromesso. Dopo aver ridisegnato al CAD la parte rovinata, il gruppo ha immediatamente pensato di riprodurlo stampandolo in 3D, ottenendo risultati sorprendenti: il pezzo prodotto si è dimostrato all'altezza dell'originale e ha permesso all'autovettura di tornare in pista per concludere le giornate di test invernali. Il CTO di UniBo Motorsport, Rosario La Rocca, ha evidenziato come quest’evento abbia fatto capire al gruppo le potenzialità di uno strumento come la stampante 3D: "penso una cosa, la progetto, la stampo e poi la installo. La mentalità di produzione sta mutando grazie alla praticità e comodità di questa nuova invenzione." http://www.stampa3d-forum.it/wp-content/uploads/2017/01/UniBo-Motorsport4-1024x680.jpg Questo episodio, seppur di rilievo, non è stato l'unico in cui il Team ha potuto sperimentare l'utilità della stampa 3D nel loro specifico settore. Il Team utilizza la tecnologia additiva per agevolare diverse attività progettuali, tra cui la verifica dei reali ingombri in vettura di componenti varie. Per esempio: convogliatori aria per il raffreddamento dei freni e il supporto per un motorino che permetterà la realizzazione di un sistema di ripartizione freno controllato elettronicamente. UniBo Motorsport, come progetto specifico per questo nuovo anno, ha in mente l'esecuzione di stampi per la laminazione di pezzi in carbonio per la vettura 2017. Con l'aiuto della loro stampante 3D Mark One potranno ottimizzare i processi progettuali e produttivi, risparmiando risorse e ottenendo benefici che, a livello competitivo, potrebbero risultare fondamentali nella riuscita della nuova stagione sportiva.
-
- settori
- ingegneria
- (and 9 più)
-
Dopo 700 anni una donna torna ad avere un volto grazie all'integrazione della stampa 3D alle tecniche di antropologia forense applicate in ambito storico-archeologico. Quello che vi presenterò oggi è il risultato di un lavoro minuzioso, che ha visto la partecipazione dell'azienda italiana 2be3D srl nelle attività di realizzazione, ottimizzazione e post-produzione del modello stampato in 3D del cranio di Hari. Archeologia e stampa 3D - Il caso Hari Più di 700 anni fa, a Vronen, località a 19 chilometri da Amsterdam, si fronteggiarono due eserciti: da una parte Olandesi e Zelandesi guidati da Jan III, dall’altra i Frisoni, popolo che combattè per la propria libertà. A fine battaglia si contarono circa 3500 Frisoni morti: praticamente l’intera popolazione maschile adulta perì in quella battaglia. Risale al 1991 la scoperta delle vittime del massacro olandese, che avvenne non solo durante, ma anche dopo la battaglia di Vronen, tra cui cadaveri con ferite alle gambe e un cranio. Nell’ambito di un progetto costituito tra 2be3D srl, Virtutim srls e Open State Foundation, la ricostruzione facciale del cranio ritrovato si è conclusa il 21 Maggio 2016. Hari, donna uccisa nel corso della battaglia di Vronen, oggi ha di nuovo un volto. Archeologia e stampa 3D - Il processo di ricostruzione facciale Il primo step consiste nel rilevamento in 3D del cranio della vittima. Per il particolare significato del reperto, è stato deciso di procedere ad una restituzione in 3D tramite fotogrammetria: sono state scattate oltre 150 foto con una Canon 60D APS-C e obbiettivo ad ottica fissa 20mm. http://www.stampa3d-forum.it/wp-content/uploads/2017/01/scan_hari-1024x294.jpg Le tracce visibili sul cranio ben testimoniano la ferocia e l’inaudita violenza degli Olandesi vittoriosi sulla popolazione frisone. Sul cranio, infatti, sono state registrate ben otto ferite di spada, sintomo di un desiderio vero e proprio di infierire sulla vittima. http://www.stampa3d-forum.it/wp-content/uploads/2017/01/cranio-1.png Il modello tridimensionale ottenuto dalla fotogrammetria, è stato poi post-prodotto e ottimizzato per essere stampato sia in tecnologia FDM a plastica ABS, sia texturizzato con tutte le sue sfumature di colore originali, in polvere di pietra, tramite tecnologia CJP. http://www.stampa3d-forum.it/wp-content/uploads/2017/01/stampa_hari-1024x286.jpg La ricostruzione del cranio facciale è stata realizzata manualmente seguendo il protocollo di Manchester, che consiste il risultato della fusione di due tecniche: quella americana, basata unicamente sull'apposizione degli spessori tissutali ricoperti di plastilina o creta, e quella russa, che ricostruisce il viso muscolo per muscolo. Il profilo del naso è stato ottenuto seguendo il metodo di George, mentre la mandibola è stata ricreata seguendo le statistiche della popolazione dell’epoca. Seguendo e unendo tra loro queste tecniche di ricostruzione è quindi possibile risalire ai tratti facciali dei nostri predecessori umani. In fine, dopo il lavoro di manodopera, il risultato è sorprendente. Ecco Hari. http://www.stampa3d-forum.it/wp-content/uploads/2017/01/ricostruzione_hari-1024x576.jpg
-
Stampare metallo non sarà più proibitivo come lo è stato fino ad oggi. Markforged è una società americana che si pone come obiettivo quello di ridurre i costi della stampa 3D a metallo, rendendola accessibile a tutti abbattendone i costi. Diventata famosa per la sua prima macchina, Mark One, capace di lavorare materiali compositi a base di nylon e fibra di carbonio a fibra continua, al CES di Las Vegas presenta il modello Metal X. http://www.stampa3d-forum.it/wp-content/uploads/2017/01/Markforged-Metal-X.jpg La novità di Metal X sta nella tecnologia utilizzata e nei materiali disponibili: parliamo di acciaio 303, alluminio 6061, acciaio 7-4, acciaio D-2, acciaio A-2, Inconel 625, Titanio, Ergal, da lavorare su uno volume di stampa di 220 x 250 x Z 200 mm. Markforged Metal X - La tecnologia Metal X si basa sull'Atomic Diffusion Additive Manufacturing, una tecnologia che prevede la deposizione di un polimero utilizzato come materiale di supporto, contenente polveri metalliche. Il modello, una volta realizzato, sarà quindi composto da una base plastica che verrà disciolta all'interno di un forno ad alte temperature. In questo modo, resterà a vivo solamente il pezzo composto dalle polveri metalliche che, all'interno del forno, si uniscono tra loro, sinterizzando. Il risultato dovrebbe essere vicino ai pezzi realizzati con le tecnologie di stampa 3D a metallo più conosciute. Il costo di Metal X dovrebbe aggirarsi sui 100.000 $, una cifra nettamente più bassa rispetto la concorrenza nel settore dei metalli. http://www.stampa3d-forum.it/wp-content/uploads/2017/01/metal-X-markfroged-e1484294962645.jpg
-
- stampanti 3d
- settori
- (and 8 più)
-
Alla Maker Faire Rome ci siamo imbattuti nella nuova stampante 3D di Kentstrapper, Verve. Kentstrapper Verve - Carateristiche tecniche Volume di stampa: 200 x 200 x 200 Tipo estrusore: 0,4 mm all metal - Titan di e3D Piano riscaldato: 50 - 100°C Display 2,8 pollici COnsumo: 360 watt max Velocità di stampa : 10 -300 mm/s Prezzo: non definito http://www.stampa3d-forum.it/wp-content/uploads/2016/10/kentstrapper-verve-6.png Segue pubblicazione del comunicato stampa Kentstrapper ha presentato oggi la stampante 3D Verve, questo prodotto è l’ultimo modello realizzato dall’azienda, in cui si fondono insieme tecnologia avanzata e semplicità di utilizzo. In questa stampante 3D sono stati introdotti sistemi per facilitare l’interazione uomo - macchina, tra i quali la calibrazione automatizzata, l’interfaccia Narwhal, il Filament Guardian, il Phoenix system e il caricamento del file di stampa direttamente da pennetta usb. Tutte queste caratteristiche rendono il nuovo prodotto in linea con le prestazioni e l’attenzione al design del brand Kentstrapper. http://www.stampa3d-forum.it/wp-content/uploads/2016/10/Kentstrapper-Verve.pnghttp://www.stampa3d-forum.it/wp-content/uploads/2016/10/kentstrapper-verve-3.png CALIBRAZIONE AUTOMATICA - Giusto il tempo di iniziare La parte più complicata nell’utilizzo di una stampante 3D risiede nella procedura di calibrazione del piatto di stampa. Abbiamo cercato la soluzione a questo problema e abbiamo dotato la stampante 3D Verve di un sistema automatizzato di calibrazione. Appena la accederai sarai in grado di stampare senza dover effettuare nessuna procedura di calibrazione NARWHAL Una vista dinamica Narwhal è un interfaccia dinamica dove icone colorate con raffigurazioni permettono all’utente di accedere ai comandi in modo semplice e veloce. Nessuna manopola, nessun click, il display touch screen da 2,8 pollici permetterà di gestire tutto con il semplice tocco delle dita. Con Narwhal potrai avviare le tue stampe direttamente da pennetta usb. http://www.stampa3d-forum.it/wp-content/uploads/2016/10/Kentstrapper-verve-2.png FILAMENT GUARDIAN - Finisce il filo ma non la stampa Se il filamento termina non dovrete più rinunciare al vostro oggetto. La stampante 3D VERVE è in grado di capire se il filamento è terminato e di salvare il processo di stampa per poi essere riavviato, una volta aver ricaricato il filamento. PHOENIX SYSTEM - Interrompi. Arresta. Riprendi quando vuoi. L’interruzione di corrente non causerà mai più il fallimento della vostra stampa. La stampante 3D VERVE è in grado di capire se viene privata dell’alimentazione e di salvare il processo di stampa. Sul display della stampante apparirà un messaggio che notifica l’assenza di alimentazione e non appena l’alimentazione ritornerà la stampante 3D ripartirà da dove si era interrotta. Questo sistema permette anche di gestire il processo di stampa, può essere messo in pausa o arrestato per poi riprenderlo in un secondo momento.
-
- stampanti 3d
- settori
-
(and 5 più)
Taggato come: