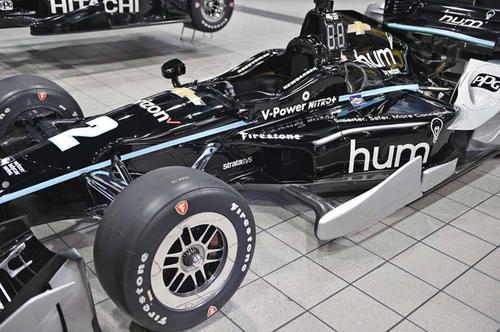
Stratasys Fortus carbonio - Le richieste del mercato
Di recente, il materiale composito ha assistito a una crescita sul mercato anno dopo anno dall ‘8 al 12%. Le applicazioni composite in fibra di carbonio e i polimeri rinforzati in fibra di carbonio sono considerati tecnologie energetiche pulite dal Dipartimento dell’Energia degli Stati Uniti d’America in quanto consentono di produrre oggetti più leggeri, i quali riducono il consumo di energia. Si stima che una riduzione del 10% del peso del veicolo consenta di ridurre dal 6 all’8% il consumo di carburante.
STAMPA 3D METALLO “DIRECT METAL PRINTING”: COS’È E COME FUNZIONA
Stratasys è stata una delle prime aziende a offrire un composito caricato a fibra di carbonio per la fabbricazione additiva, ma in precedenza offriva il materiale solo sulle stampanti 3D di produzione di fascia alta, tra 200.000 e 350.000 euro. “I nostri clienti spingono per un accesso semplificato alla fibra di carbonio”, afferma il vicepresidente senior di Stratasys, Pat Carey. “Ci hanno detto che desiderano una soluzione a basso costo ma in un sistema affidabile di livello industriale. È per questo che stiamo offrendo un sistema più accessibile, basato sulla nostra piattaforma Fortus 380. Poiché la 380mc CFE è dedicata esclusivamente al Nylon 12 caricato a fibra di carbonio e a un altro materiale, siamo in grado di offrirla al prezzo più basso di qualsiasi altra stampante industriale”.
“Da molti anni, il settore della fabbricazione additiva assiste alla necessità di una serie di macchine diverse per produrre parti in materiali compositi a resistenza elevata” afferma Terry Wohlers di Wohlers Associates, un’azienda di consulenza nel settore della fabbricazione additiva. “Spero che la recentissima macchina di Stratasys consentirà di soddisfare questa esigenza offrendo parti resistenti in fibra di carbonio e Nylon 12”.
POLIAMMIDE 11 – MATERIALE IN POLVERE PER LA STAMPA 3D A SINTERIZZAZIONE LASER
Il team Penske utilizza l’FDM per produrre prototipi e parti finali nel materiale composito Nylon 12 caricato a fibra di carbonio sia per le auto da corsa dell’IndyCar che per quelle della NASCAR. Il team ha utilizzato di recente il composito per produrre un alloggiamento per lo specchietto per i team di corsa della NASCAR. Dopo aver progettato l’alloggiamento, gli ingegneri hanno personalizzato il progetto per ognuno dei piloti dei bolidi, creando le parti finali in composito tramite FDM. Il materiale basato su fibra di carbonio ha consentito al team Penske di produrre alloggiamenti per specchietti leggeri con elevata resistenza agli urti e alta rigidità, caratteristiche fondamentali nel settore delle corse. La rigidità del composito è vantaggiosa soprattutto quando si creano parti con pareti sottili, che non devono flettersi sotto i carichi aerodinamici prodotti sulla pista.
Le applicazioni additive per il Nylon 12 caricato a fibra di carbonio possono includere:
Prototipazione funzionale delle parti in composito o in metallo
Cicli di produzione brevi in un materiale a resistenza elevata
Produzione di strumenti di assemblaggio leggeri per migliorare l’ergonomia e alleviare la fatica degli addetti
Sostituzione di parti metalliche con compositi leggeri e resistenti
Stratasys prevede che i più rapidi ad adottare la stampante 3D Fortus 380 CFE saranno le aziende che realizzano strumenti e staffaggi e le aziende dei settori automobilistico, delle attrezzature per gli sport ricreativi, marino, ortesico e protesico, della difesa, aerospaziale, delle attrezzature mediche, del petrolio e del gas.
Come una parte in plastica rinforzata con fibra di carbonio stampata a iniezione, il Nylon 12CF di Stratasys è costituito per il 35% di frammenti di fibra di carbonio e presenta un rapporto rigidità/peso elevato, superiore a qualsiasi parte stampata in 3D FDM o FFF.Stratasys Fortus 380mc CFE si basa su una piattaforma comprovata che produce parti caratterizzate da precisione dimensionale ripetibile. Le parti non mostrano curvatura o restringimento apprezzabile e mantengono una stretta tolleranza. Il Nylon 12CF Stratasys è fino a quattro volte più resistente rispetto all’alternativa economica sull’asse delle X e delle Y e mantiene le proprietà meccaniche a una temperature superiore del 40%.
STRATASYS PER LA STAMPA 3D DENTALE: LA NUOVA J700 DENTAL
Stratasys Fortus 380mc CFE crea parti dello spessore di 0,254 mm (0,010 pollici). Il sistema è inoltre compatibile con la termoplastica ASA, che è in grado di produrre spessori degli strati di 0,127 mm (0,010 o 0,005 pollici). La camera di costruzione della stampante 3D misura 355 x 305 x 305 mm (14 x 12 x 12 pollici). Offre la rimozione del materiale di supporto idrosolubile, che elimina la necessità di manodopera per la rimozione dei supporti. Di conseguenza, consente la creazione di geometrie sottili e intricate, che sarebbero impossibili senza il materiale di supporto solubile, in quanto le caratteristiche sottili verrebbero distrutte durante la pulizia oppure la rimozione del materiale di supporto dalle geometrie intricate potrebbe risultare troppo laboriosa o addirittura impossibile.
La stampante 3D Fortus 380mc edizione in fibra di carbonio sarà visibile presso lo stand Stratasys in occasione del TCT #H36 dal 25 al 27 settembre al NEC di Birmingham.
Vuoi saperne di più? Iscriviti al nostro forum, la community sarà felice di aiutarti!
Resta aggiornato sulle ultime novità, seguici su Facebook e Twitter.
- Leggi di più...
-
- 0 commenti
- 1.261 visite